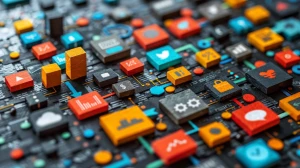
Industrial Robots: The Invisible Workforce Shaping the Future of Automation
Discover how industrial robots are transforming manufacturing with unmatched precision, efficiency, and AI innovation. Explore their benefits, challenges, and what the future holds for automation.
by Niranjani
Updated Feb 03, 2025
On This Page
- The Evolution of Industrial Robots. From Clunky Machines to Cognitive Collaborators
- Why Factories Can’t Resist the Robot Revolution. Key Benefits
- Beyond Speed and Precision. Unexpected Advantages of Automation
- Navigating the Challenges. Costs, Complexity, and Workforce Shifts
- The Next Frontier. AI, Swarm Robotics, and Self-Healing Systems
- Humans and Robots. Redefining Collaboration in the Smart Factory Era
- Sustainability Meets Automation. The Green Advantage of Industrial Robots
Picture a factory floor where the hum of machinery is punctuated not by human voices, but by the rhythmic whir of robotic arms assembling products with pixel-perfect accuracy. This is not a scene from a sci-fi film—it’s the reality of today’s manufacturing landscape, where industrial robots have emerged as the silent, tireless backbone of global production. These machines, once confined to repetitive tasks in automotive assembly lines, now wield artificial intelligence, advanced sensors, and machine learning to revolutionize industries from pharmaceuticals to aerospace.
Their impact is profound: they’re closing labor gaps, slashing waste, and enabling innovations once deemed impossible. Yet, their story isn’t just about replacing humans—it’s about reimagining collaboration. As robots handle dangerous, mundane, or precision-critical work, human workers are freed to focus on creativity, strategy, and problem-solving. The result? Factories that are faster, safer, and more sustainable than ever before.
But this transformation isn’t without its tensions. As the invisible workforce grows, questions about ethics, job displacement, and the future of human expertise loom large. How do we balance efficiency with empathy? Can machines truly become partners in progress? Dive into the world of industrial robots, where the future of automation is being written—one algorithm, one weld, and one innovation at a time.
The Evolution of Industrial Robots: From Clunky Machines to Cognitive Collaborators
Trace the journey of industrial robots from rudimentary mechanical arms to intelligent, AI-driven systems capable of learning and adapting.
- 1960s Origins: The first Unimate robot welded car parts in GM factories, sparking the automation revolution.
- Sensor Revolution: Modern robots use LiDAR, vision systems, and force sensors to “see” and “feel” their environment.
- AI Integration: Machine learning lets robots optimize tasks in real-time, like sorting irregularly shaped items.
- IoT Connectivity: Robots now share data across global supply chains, enabling synchronized production lines.
- Cobots Emerge: Collaborative robots like UR10 work safely alongside humans, merging flexibility with brute strength.
Why Factories Can’t Resist the Robot Revolution: Key Benefits
Dive into the tangible advantages driving the adoption of industrial robots.
- Unmatched Productivity: Robots work 24/7 without fatigue, slashing production cycles by up to 50%.
- Surgical Precision: Error rates drop to near-zero in tasks like microchip assembly or pharmaceutical packaging.
- Cost Savings: Automating repetitive tasks reduces labor expenses and costly rework from human error.
- Safety First: Robots handle hazardous tasks—welding, toxic material handling—cutting workplace injuries by 72% (OSHA).
- Labor Gap Fix: With aging workforces, robots fill gaps in industries like automotive and electronics.
Beyond Speed and Precision: Unexpected Advantages of Automation
Industrial robots aren’t just about efficiency—they enable data-driven decision-making, waste reduction, and customization at scale.
- Data Goldmines: Sensors on robots collect real-time analytics, predicting bottlenecks and optimizing workflows.
- Zero-Waste Goals: AI-driven robots trim excess material use, reducing waste by 30% in industries like textiles.
- Mass Customization: Robots enable small-batch production, letting brands offer personalized products at scale.
- Agility Boost: Automated lines can pivot from making car parts to medical devices in hours, not weeks.
- Innovation Catalyst: Freed from mundane tasks, engineers focus on R&D for next-gen products.
Navigating the Challenges: Costs, Complexity, and Workforce Shifts
While robots promise transformation, their integration isn’t without hurdles.
- High Upfront Costs: A single robotic cell can cost $100k+, though ROI often justifies the spend in 2-3 years.
- Integration Headaches: Retrofitting legacy factories with robots requires costly IT/OT infrastructure upgrades.
- Skills Gap: Engineers need training in robot programming, AI, and cybersecurity to manage advanced systems.
- Ethical Dilemmas: Automation could displace 20M manufacturing jobs by 2030, demanding reskilling initiatives.
- Maintenance Demands: Downtime from software glitches or part failures remains a critical pain point.
The Next Frontier: AI, Swarm Robotics, and Self-Healing Systems
Peer into tomorrow’s factories, where robots collaborate in swarms and predict maintenance needs.
- Predictive AI: Robots like Siemens’ “self-aware” machines diagnose motor wear and order repairs autonomously.
- Swarm Intelligence: Drone fleets and mini-robots coordinate to assemble large structures, inspired by ant colonies.
- Self-Healing Tech: Materials with microcapsules repair minor cracks, extending robot lifespans by decades.
- 5G Acceleration: Ultra-low latency lets robots communicate instantly, enabling real-time remote control.
- Digital Twins: Virtual replicas of robots simulate scenarios, slashing testing time for new workflows.
Humans and Robots: Redefining Collaboration in the Smart Factory Era
Robots aren’t replacing humans—they’re redefining their roles.
- Cobot Synergy: ABB’s YuMi assists with delicate tasks like watchmaking, guided by human intuition.
- Upskilling Surge: Workers transition to roles like “robot trainer” or data analyst, earning 25% higher wages.
- Danger Zone Masters: Robots handle tasks in extreme temperatures or radiation zones, keeping humans safe.
- Creativity Unleashed: With robots managing assembly lines, designers and strategists drive innovation.
- Trust Building: Mixed-reality interfaces help workers visualize robot workflows, reducing resistance to change.
Sustainability Meets Automation: The Green Advantage of Industrial Robots
From energy-efficient operations to minimizing material waste, robots help industries go green.
- Energy Savers: Robots like FANUC’s “Eco-Mode” models cut power use by 15% during idle periods.
- Circular Economy: Precision robots disassemble old electronics, recovering 98% of rare metals for reuse.
- Waste Warriors: AI vision systems spot defects early, reducing scrap rates in food production by 40%.
- Low-Carbon Logistics: Autonomous electric forklifts cut emissions in warehouses by 60% vs. diesel counterparts.
- Lifecycle Efficiency: Robots built with recyclable materials slash e-waste, aligning with EU sustainability laws.
Industrial robots are no longer just tools—they’re partners in building faster, smarter, and greener industries. By embracing their potential while addressing ethical and logistical challenges, businesses can craft a future where humans and machines thrive together.